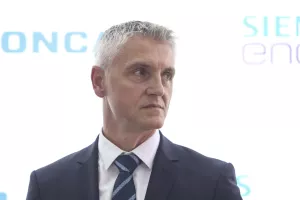
Inteligentna elektrifikacija kakvu omogućuje Siemens
Elektrifikacija ima velik potencijalni utjecaj na dekarbonizaciju jer omogućuje čistoj struji iz obnovljivih izvora pokretanje procesa za koje su se ranije upotrebljavale tehnologije s velikim emisijama poput dizelskih generatora. No, električnom energijom treba učinkovito upravljati, a tu Siemens nudi dobra digitalna rješenja
U Siemensu su identificirali tri poluge koje mogu potaknuti smanjenje emisija i dekarbonizaciju u procesnoj i proizvodnoj industriji, koja troši mnogo energije – čak trećinu ukupne potrošnje. Prije svega, tu je unošenje veće fleksibilnosti u korištenje energije, primjerice korištenjem virtualnih elektrana i rješenja za pohranu.
Osim toga, potrebno je digitalizirati pogonske procese koji mogu omogućiti učinkovito korištenje energije, što se može postići korištenjem IoT uređaja (internet stvari), senzora i softvera. I posljednje, potrebna je inteligentna elektrifikacija u svim pogonskim procesima, što ima najveći potencijal za dekarbonizaciju.
Pritom kod elektrifikacije treba voditi računa o energetskoj opskrbi industrijske lokacije, npr. potencijalnom korištenju obnovljive energije iz vjetroelektrana, solarnih elektrana i hidroelektrana bez emisije CO₂ te energetskom menadžmentu na lokaciji, npr. u obliku softverskog upravljanja potražnjom.
'Pametna' elektrifikacija
Elektrifikacija ima veliki potencijalni utjecaj na dekarbonizaciju jer omogućuje čistoj struji iz obnovljivih izvora pokretanje procesa za koje su se ranije upotrebljavale tehnologije s velikim emisijama poput dizelskih generatora. Drugim riječima, procesi se u potpunosti mogu odvijati bez emisija ako se za njihovo pokretanje upotrebljava obnovljiva energija. Pritom elektrifikacija otvara vrata digitalizaciji i inteligentnijoj elektrifikaciji, što omogućuje energetsku učinkovitost te pogonsku otpornost i optimizaciju postrojenja.
Učiniti elektrifikaciju 'pametnom' znači implementirati senzore i platforme za internet stvari koji mogu prikupiti ogromne količine podataka. Podaci se akumuliraju te ih analiziraju algoritmi i softver kako bi operaterima postrojenja pomogli u tome da identificiraju mogućnosti povećanja učinkovitosti u energetskom sustavu postrojenja i u pogonu općenito.
To, između ostalog, vodi do optimizirane proizvodnje i niske potrošnje struje. Istodobno, moguće je rano prepoznati situacije koje mogu negativno utjecati na učinkovitost sustava, poput prekida rada strojeva. Drugim riječima, digitalizacija omogućuje stvaranje digitalnog blizanca energetskog sustava tvornice. U kombinaciji s industrijskom automatizacijom korisnici na taj način mogu testirati niz operativnih scenarija. Svrha je testiranja optimalna koordinacija sustava i usluga, što pridonosi nižim stopama pogrešaka i nižim troškovima projektiranja, izgradnje i održavanja.
Što su učinili u Vetropacku
Primjeri iz prakse pokazuju prilike koje se pružaju industrijskim poduzećima. Jedan od njih nalazi se i u Hrvatskoj – Vetropack Straža, koja je dio švicarskoga koncerna Vetropack Group, vodećega europskog proizvođača staklene ambalaže za industrije hrane i pića. Budući da je proizvodnja stakla iznimno energetski i troškovno zahtjevan proces, Vetropack je kod implementacije sustava za upravljanje i nabavu energije morao uzeti u obzir niz strateških, ekonomskih i tehničkih čimbenika. Sve to ne bi bilo moguće bez korištenja profesionalnih softverskih alata.
Tako se kompanija danas koristi sustavom za upravljanje energijom Simatic Energy Manager PRO, koji uključuje napredne module za strukturiranu nabavu energije, razvijene za Vetropackove specifične potrebe na temelju opsežnih specifikacija. Nakon što je projekt započeo 2017. godine, Siemens i Vetropack su pilotirali sustav u austrijskoj tvornici u Kremsmünsteru 2019., prije nego što su ga ugradili u postojeću automatizacijsku (DCS Simatic PCS 7) i IT infrastrukturu u svim ostalim tvornicama, počevši od tvornice u hrvatskom mjestu Straža.
Za dvije godine, kad završi uvođenje u cijeloj Grupi, tvrtka će imati potpunu transparentnost svih relevantnih vrijednosti potrošnje energije, medija i pripadnih troškova (ponajprije plina, struje, vode i komprimiranog zraka), kao i emisija CO2.
Koriste se i pivari i metalci
Osim toga, jedna finska pivovara trenutačno, u suradnji s investicijskim konzorcijem u kojem sudjeluje i Siemens, gradi umreženi baterijski sustav pohrane električne energije (BESS). Uz napredan softver, koji upravlja pogonom energetskog sustava, postrojenje radi kao virtualna elektrana (VPP) koja optimizira potrošnju struje pivovare, ali i omogućuje trgovanje energijom s operaterom mreže. Na taj se način poboljšava energetska učinkovitost postrojenja, ali se i dobiva novi izvor prihoda jer operater mreže daje naknadu za redukciju potražnje energije u određenim razdobljima. VPP softver i baterijski spremnici na lokaciji omogućuju taj proces.
Tu je i drugi primjer španjolskog proizvođača metalnih komponenti za automobilsku industriju. Instalacijom brojača električne energije i komunikacijskih rješenja u kombinaciji s big data analizama u 15 tvornica smještenih u šest zemalja tvornica je uspjela identificirati potencijale za unaprjeđenje i provesti odgovarajuće mjere koje su smanjile potrošnju električne energije za 15 posto na godišnjoj razini, a emisiju CO₂ za 14.000 tona na godinu. Na ovakvim praktičnim primjerima jasno je kako industrija može učinkovito upravljati potrošnjom energije, a za postizanje tog cilja najbolji je put inteligentna elektrifikacija kakvu omogućuju u Siemensu.